about
Comprehensive Testing Solutions for Metallic Materials
Metcut and Metcut France test over 40,000 metallic specimens a year. Whether it be an ASTM standard test or a custom defined procedure, we have the experience, trained personnel and equipment to meet your testing needs.
Low and High Cycle Fatigue
Our servo-hydraulic and rotating mass fatigue machines measure longitudinal strain and high-cycle fatigue properties at temperatures ranging from -320°F to 2400°F in various environments. Metcut uses its large number of testing machines for high production testing of a variety of sample geometries and materials in various environments.
Standard test coupon geometries are M12 through M18, 7/16-UN through 3/4-UN and 0.4-in. through 0.75-in.-diameter buttonhead shank bars. We also provide sheet specimen strain control testing to 0.055-in. minimum thickness and 2000°F depending on material characteristics.
Standard fatigue tests are conducted utilizing servo-hydraulic equipment conducted in constant strain or load amplitude control modes in accordance with ASTM E-606, and E-466.
We conduct tests at 0.1- to 2-Hz. frequencies for longitudinal strain control tests, and 0.01- to 90-Hz. for axial load control tests. We also perform creep and stress relaxation tests in servo-hydraulic machines under very precise control from one to several hundred hours.
Elevated temperature tests are conducted with either resistance furnaces or induction field generators, depending on the material characteristics. We conduct cryogenic tests at any temperature between 32°F and -320°F using liquid Nitrogen as a cooling medium. We routinely maintain test temperatures within the sample gage section at 1% of the test temperature.
Several Sonntag universal test machines are available to conduct testing at high displacement amplitudes incurred during cantilever bending tests. R.R. Moore and Krouse rotating beam tests are available in four-point and cantilever bend modes at room and elevated temperatures.
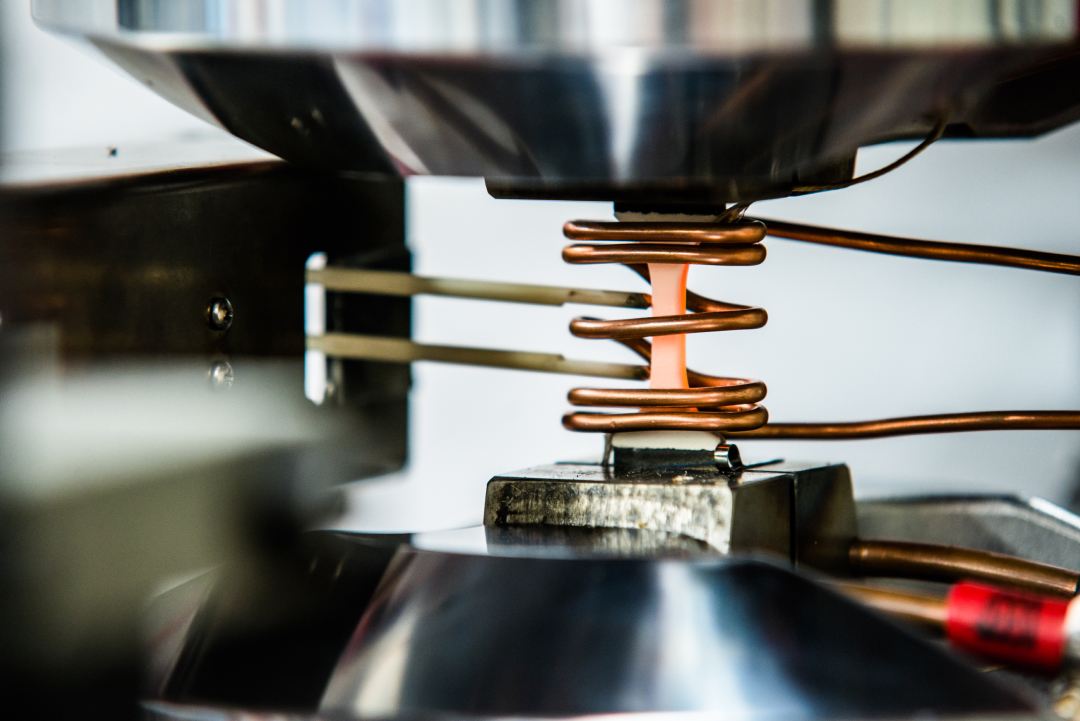
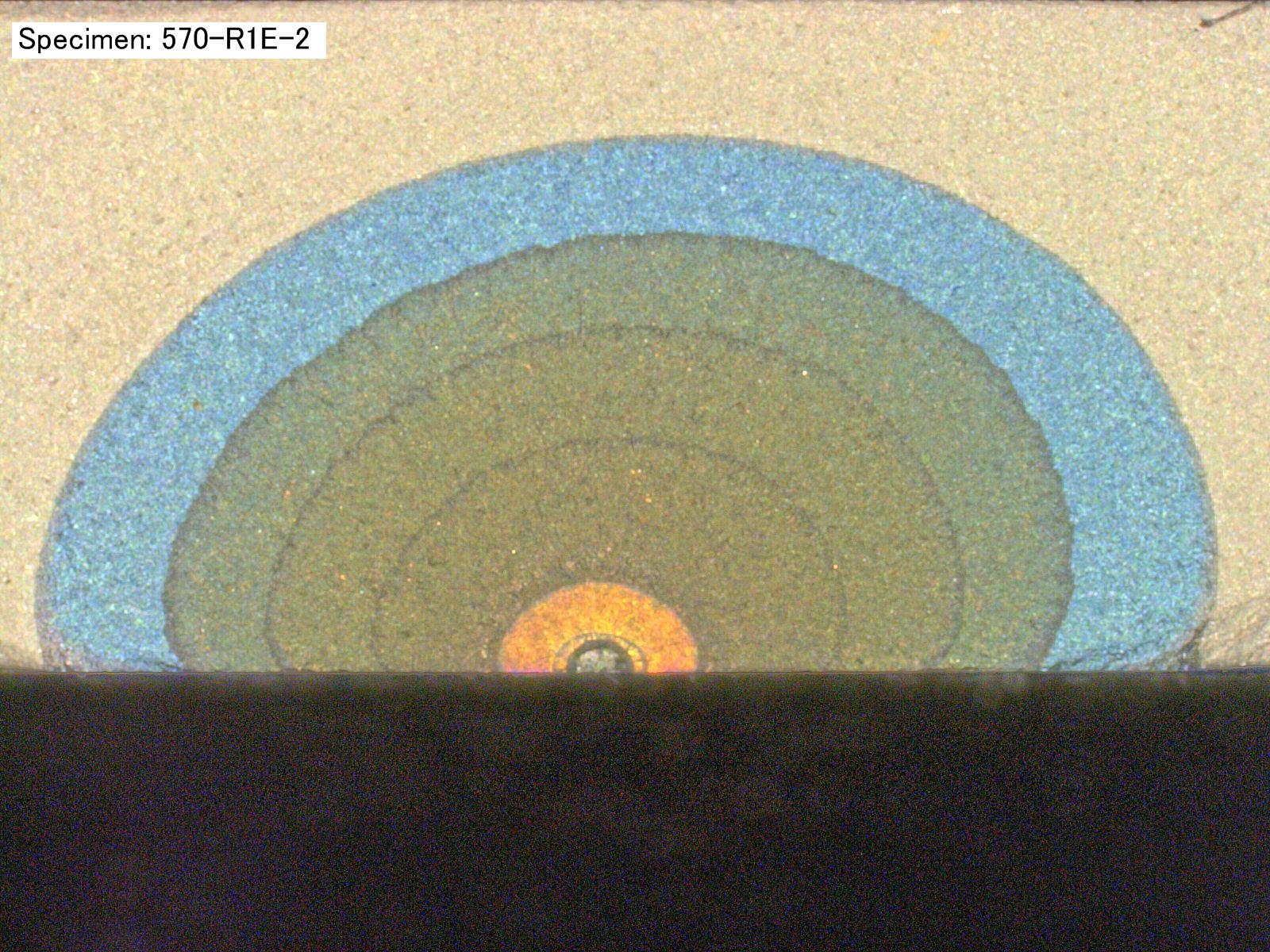
Fracture Mechanics & Crack Propagation
Fracture toughness and fatigue crack growth evaluation have been an integral part of Metcut Research material testing services since the development of standardized testing specifications. Today we utilize the finest systems available to perform these testing features supported by state-of-the-art data acquisition and machine automation.
Metcut continues to expand its DC Electric Potential Drop (EPD) testing capability. Our FTA® systems provide automated test control and data acquisition for crack growth and fracture toughness testing. Careful placement of monitoring probes permits test gage lengths as small as 0.035 in.
Fracture Mechanics & Crack Propagation
ASTM E-647
Fatigue crack propagation using the compliance method and the potential drop method of crack measurement. Specimens supported include Compact Tension (CT), Middle Tension (MT), Single Edge Notch (SEN), Single Edge Bend (SEB), Extended Compact Tension (ECT), various corner crack designs, and surface flaw designs. Metcut Research routinely performs testing from cryogenic temperatures to 1600°F (871°C). We also support steady-state cyclic fatigue, as well as dwell-time fatigue. Fatigue crack growth rates from the threshold regime to the critical region are typically developed, using constant load as well as K-controlled parameters.
ASTM E-1457
Static creep crack growth rate measurements using the potential drop method. The compact tension specimen is the standard specimen design for this specification. We typically perform this experiment at elevated temperatures.
ASTM E-399
Plane strain fracture toughness testing. We use the Compact Tension (CT) design, Single Edge Bend (SEB), Arc-Shaped Specimens, and the Disk-Shaped specimens. We typically perform pre-cracking using the compliance technique. Testing temperature ranges from cryogenic regions to 1600°F (871°C).
ASTM E-1820
Elastic-plastic fracture toughness testing using the J-Integral technique. We typically perform this experiment using the Compact Tension (CT) design or the Single Edge Bend (SEB) specimen. Both the compliance technique and potential drop method of crack measurement is supported. Metcut Research employs the single specimen unloading technique to evaluate crack length measurements.
ASTM E-561
Fracture resistance testing using the R-Curve (resistance curve) technique. Typically the specimen design of choice is the Compact Tension (CT) or the Middle Tension (MT). We perform testing using the compliance technique as well as the potential drop method of crack measurement. ASTM E-1290 – Fracture toughness testing using the Crack Tip Opening Displacement (CTOD) measurement method. This experiment is typically performed using the compliance technique on all the standard-geometry, fracture toughness specimens.
ASTM E-1304
Plain-strain fracture toughness testing using the short rod or short bar specimen design. We use this specification primarily for brittle materials.
Creep & Stress Rupture
Metcut is equipped with 146 static frames located at our Cincinnati – Carillon facility, controlled and monitored by a computerized creep system. Eighteen frames are in-line direct load to accommodate low load tests. The remaining frames are lever-loaded systems with various load capabilities up to 30,000 pounds.
Virtech® computer-controlled systems, installed across our creep and stress rupture frames, feature a Windows-based host computer and local operator console for each pair of test frames. We can handle data collection and machine control at the local console, plus store and retrieve test specifications from the host computer.
The local microprocessor controls each frame and logs temperature and creep data. Tests can continue uninterrupted even if there is a problem with the host computer. We can generate reports anytime during or after a test for convenient customer updates throughout testing.
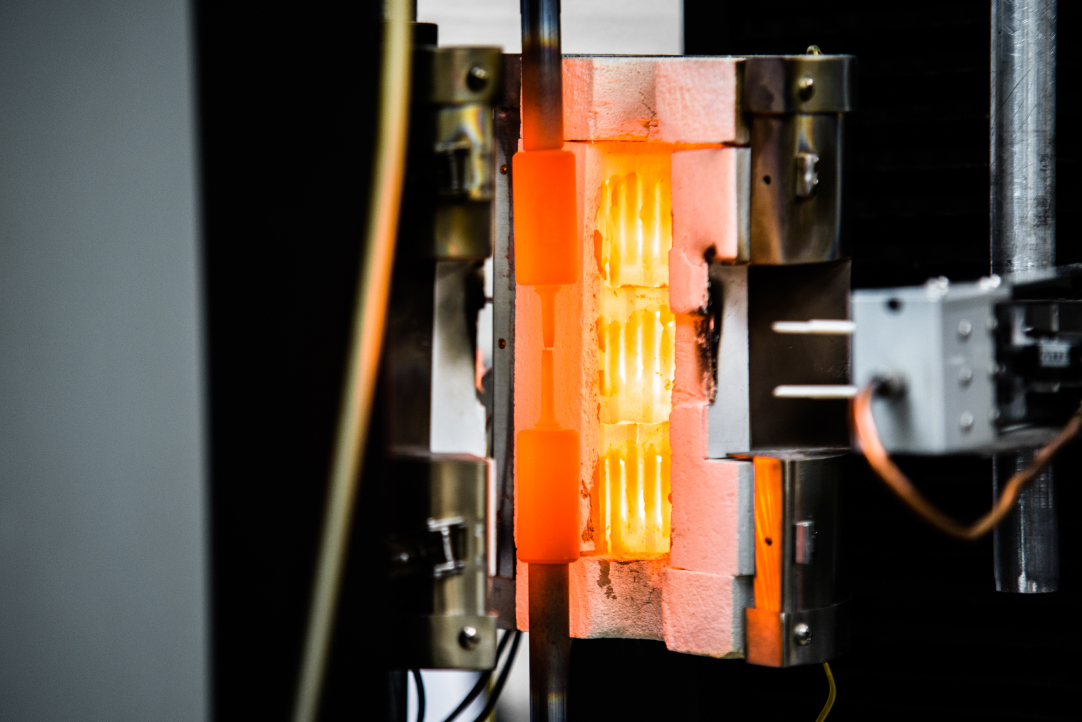
Tensile
Metcut conducts tensile, compression, and flexural tests on a wide variety of metallic, intermetallic and materials in air at temperatures ranging from -320°F to 2200°F.
Our Tensile Testing Lab features two computerized Instron® 4505 electro-mechanical test machines of 20,000-lb capacity with MTS Test Works control packages. Test data is stored at Metcut and is readily available in text format for customers who wish to perform their own data analysis. We also use a Satec Electro-Mechanical tensile machines of 50,000-lb capacity also with MTS Test Works control.
Torsion
Torsional testing is typically conducted on metallic and composite/metallic drive shaft components, shear segment drive components, bio-mechanical constructs and turbine shaft materials.
Torsional fatigue and torsional shear testing is conducted with a variety of test machines in the laboratory. Fully reversed torque through 20K lbf/inand unidirectional torque through 1,000K lbf/in testing can be conducted typically to 3 Hz. In addition, our test temperature range is from –65 °F through 1200 °F in a laboratory air environment.
Our strain gage capabilities can also be utilized to provide strain analysis during sample or component torque testing. Our capabilities have recently been expanded with a 50Kip axial / 20K lbf/in axial Torsion fatigue machine. This MTS fatigue machine is capable of varying phase cyclic fatigue testing, conducted in axial load/torque or axial strain/shear control.
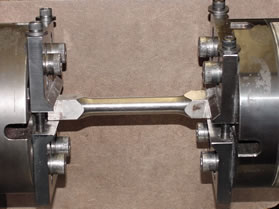
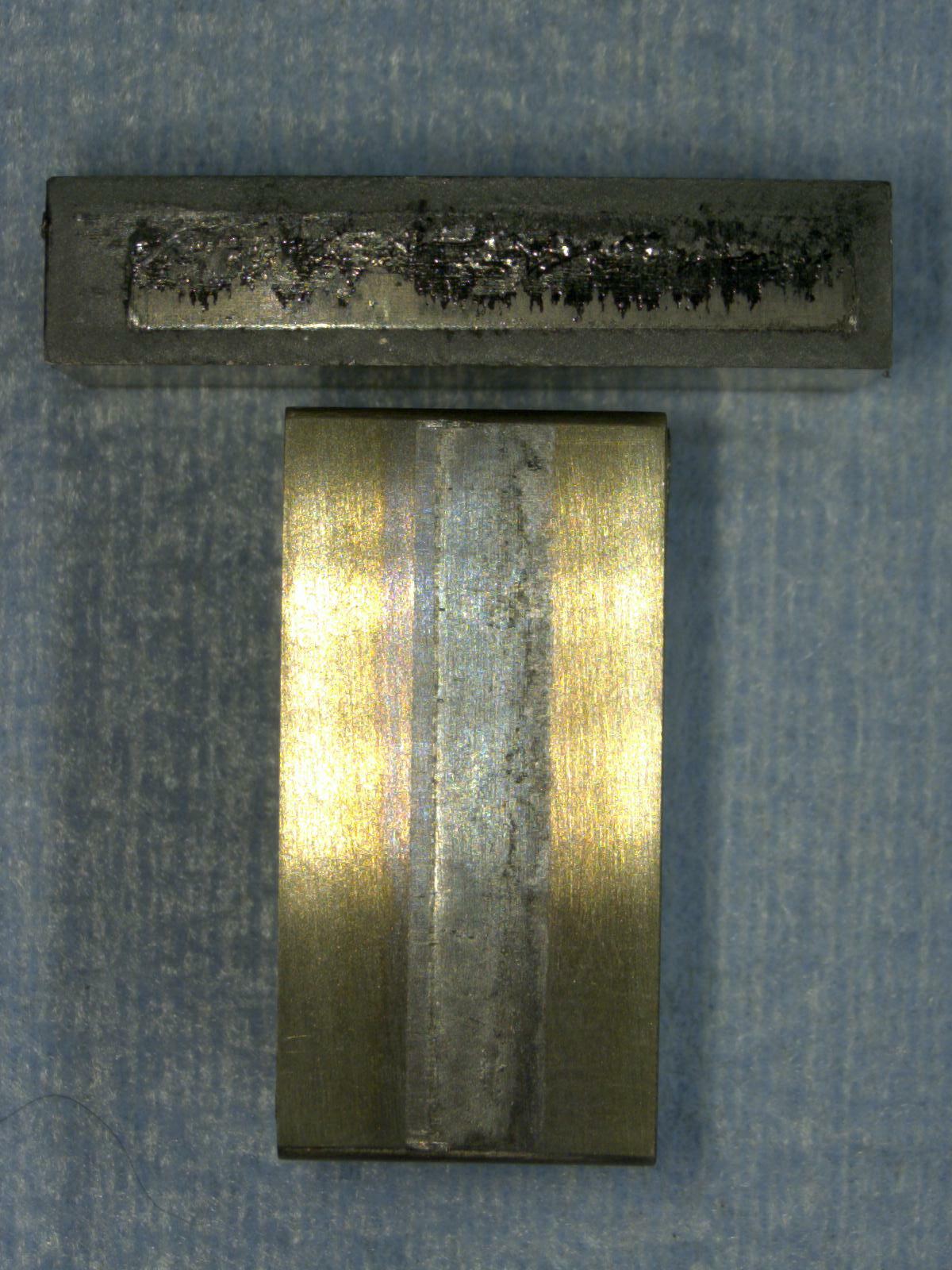
Friction and Wear
Metcut features several test machines for conducting sliding and fretting wear from 1 to 30 Hz. in short-stroke, high-temperature conditions. We conduct wear testing on a variety of equipment, but primarily with a moving shoe on a stationary block test interface.
Typical sliding wear test capabilities are temperatures of 75°F to 1800°F, test stresses up to 120 ksi depending on the material performance, and stroke ranges of 0.002 in. to 0.25 in. Sliding wear tests usually are conducted at cyclic frequencies of 1 Hz. due to the high crush forces.
Typical fretting wear test capabilities are temperatures of 75°F to 1100°F, test stresses up to 3 ksi depending on material performance, and stroke ranges of 0.002 in. to 0.010 in. These tests typically are conducted at 30 Hz.